Scientific Review
Online ISSN: 2412-2599
Print ISSN: 2413-8835
Print ISSN: 2413-8835
Quarterly Published (4 Issues Per Year)
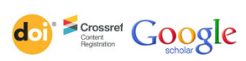
Archives
Volume 5 Number 10 October 2019
Machining Versus Molding Tolerances in Manufacturing Automotive Sealing Systems
Authors: Ben Chouchaoui ; Joe Gutierrez ; Vince Mungioli ; Kassem Ghanem
Pages: 179-184
DOI: doi.org/10.32861/sr.510.179.184
Abstract
The automotive industry has been at the forefront of converting traditional metal parts to plastics. The latter surely offer greater design freedom, opportunity for consolidation, fewer assembly operations, reduced secondary finishing, weight reduction, lower total system costs, a range of properties tailored to specific applications, the ability to withstand temperatures, immunity to most chemicals and corrosive environments. They offer processing in many colors, electrical non-conductivity (insulation from electrical shocks), good thermal breaks (“warmth-to-the-touch”), and low sound transmission (tendency to muffle noise). Nonetheless, plastics have only tapped an estimated 15% of their tremendous potential to replace metals. This is particularly to increase with newer high-performance plastics, increasing sophistication in alloying and blending technologies, and use of computer-aided design and engineering (CAD/CAE) systems. The latter enable engineers to visualize complex parts and molding tools more effectively and faster than ever before. This article identifies fundamental steps and requirements to conduct an efficient and successful conversion of metallic parts to plastics, reviewing the replacement design process from concept to production; an under-the-hood rear retainer for Ford Motor Company is detailed as a case study.
Sinthesis and Properties of Marble-Like Glass-Ceramics Using of Ash from Thermal Power Plants
Authors: Yancho Hristov Hristov ; Ganka Rumyanova Kolchakova
Pages: 173-178
DOI: doi.org/10.32861/sr.510.173.178
Abstract
Color marble-like glass-ceramic materials were obtained through thermal treatment of glasses of the system CaO-Al2O3-SiO2 by using natural materials with the introduction of waste materials - ash from thermal power plants (TPP). The melting of the glass batch was in corundum crucibles at 1450oC with an isothermal hold of 60 min. The glasses obtained was fritted in distilled water and dried for 6 hours at 100oC, then completely crushed and divided into fractions with grain size of 0.8 mm, 1.0 mm, 2 mm, 2.5 mm and over 2.5 mm. It was found that the use of ash from TPP lead to higher values of degree of transformation (crystallization) than using base composition. Values of Avramy parameter’s in the range n=1,0 ÷ 1,6 are showed that crystallization of the glass frit is largely heterogeneous and crystal growing starts from the surface. The introduction of ash from TPP to native glasses carry out to significant reduction of energy of crystallization by Ес=289 kJ/mol to Ec=221 kJ/mol. The glass-ceramic materials were obtained through a one stage crystallization - 1050÷1070оС and an isothermal hold of 60 min., colored white, yellow brown to dark brown. The main crystalline phase in glass-ceramics is β-vollastonite with needle habit, size of crystals - ĺ = 40 ÷ 120 μm and d <5 μm in quantities 37 ÷ 42%. As secondary phases depending on the amount of ash have been identified - the anorthite, gehlenite and α-quartz with prismatic habit were appeared. The obtained glass-ceramic materials have a marble-like effect and technical parameters compared with natural granite and marble and have higher values of density, micro hardness, speed grinding, bending strength and chemical resistance. That’s why they can be used in construction such as lining materials.